It’s grown locally, processed locally, 3D-printed locally, and sold locally. And its inventors think it could change how we buy just about everything.
A new bioplastic made from algae could replace oil-based plastic completely according to its inventors, potentially turning the manufacturing industry from a source of CO2 into a destroyer of the greenhouse gas. The designers behind the material imagine a world in which shops can locally produce all kinds of objects on demand, from plates to furniture, using 3D printers and the bioplastic. To demonstrate their material’s qualities, they’re producing it in small batches and using it to print designer products.
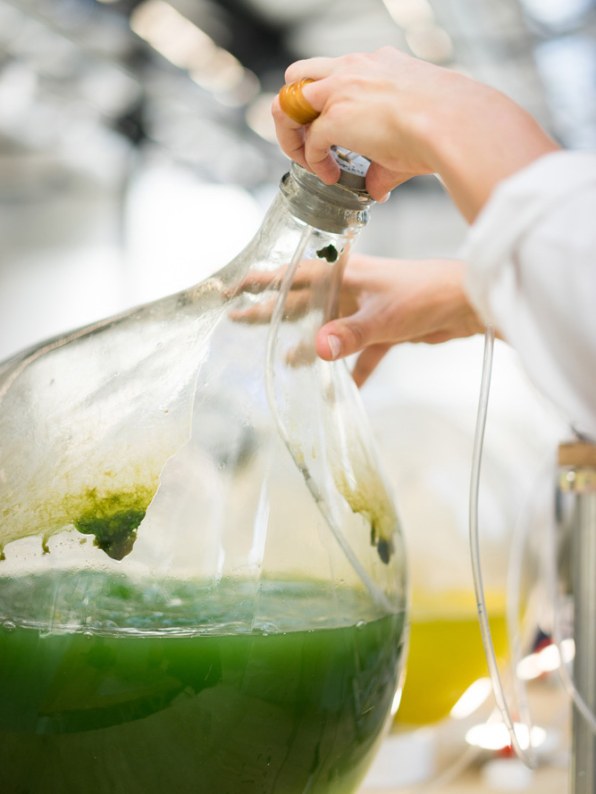
The Dutch designers Eric Klarenbeek and Maartje Dros spent three years creating their biopolymer, trying to find a solution to the problems of synthetic plastic. The latter contributes heavily to global warming and, worse, it depends on a limited, non-renewable resource as its raw material. In addition to that, plastic products get ferried from large factories all over the world into distribution centers and, eventually, retail shops, further increasing their carbon footprint.So Klarenbeek and Dros asked themselves: What if we could invent a material using locally-grown raw materials–and use it to enable a manufacturing and distribution process that remained local from start to finish?
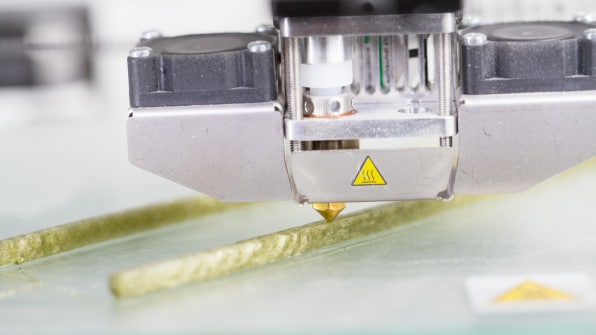
They found their answer in organic resources like mycelium, potato starch, cocoa bean shells, and, more importantly, algae.Algae are highly effective biomass generators. They’re also easy to grow and they’re great CO2 processing machines–they take this gas out of the atmosphere and the sea and turn carbon molecules into starch through photosynthesis, releasing oxygen molecules into the atmosphere as a byproduct.
Through a chemical process, Klarenbeek and Dros turn that starch into the polymer that can be used in 3D printing. According to the researchers, they “cultivate the living algae and then dry and process it to create a material that can be used to 3D print objects. In principle, we can make anything from this local algae polymer: from shampoo bottles to tableware or rubbish bins.” Project coordinator Johanna Weggelaar described the entire process via email. “The harvested microalgae is dried and powdered to be incorporated in a blend with another biopolymer used as a binder, and natural additives,” she explains. “The mix is processed in a filament for 3D printing with an extruder.” According to Weggelaar, the exact formulation is a secret, but she claims they can “achieve different textures, colors, [and] resistance playing on the different parameters of the process.” She says that right now, they’re using spirulina, a blue-green microalgae, because “there is a strong network of spirulina farmers in the South of France.”
Using these types of materials instead of oil-based plastics could effectively turn an industrial manufacturing process–a source of pollution that contributes to global warming–into a way to subtract CO2 from the atmosphere. Using algae as a raw material would turn any mode of production into a way to help the environment.
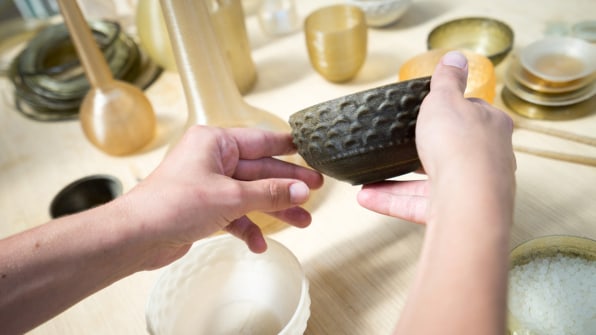
As Klarenbeek and Dros say, instead of zero emissions, the world needs negative emissions. “If we think in these terms,” they claim, “makers can bring about a revolution.” Their plan is to get local manufacturers and designers to print using this material–along with an internet-based CAD model catalog of every household item you can imagine, from tableware to laundry bins to bottles.To demonstrate this concept, they’ve been building all kinds of products at the atelier LUMA, in Arles, France. But for them], that’s just the beginning. The next step is to build a large decentralized network of object manufacturing and sale shops. Weggelaar told me that they are investing “in research around this project during the next months to test the formulations, develop the use of locally grown algae, and improve the mechanical and aesthetic properties of the material.”
They call this network the 3D Bakery, and they hope it will be fully armed and operational in a decade. Eventually, they envision their bioplastic taking over “everything”–a hopeful but complicated goal, since there are myriad specialized polymer material formulations for myriad applications. I have no doubt that eventually, we’ll get there. But 10 years may be a bit ambitious.