[Image: courtesy University of Maryland]
It could be a breakthrough for everything from airplane manufacturing to architecture.
Is wood the next advanced material?
Scientists at the University of Maryland reported last week that they’ve discovered a way to treat wood to make it 12 times stronger than natural wood and 10 times tougher. According to Liangbing Hu, one the lead researchers in the paper published in Nature, their wood is so strong and durable that it can compete with steel, titanium alloys, and even carbon fiber–but at an infinitely much lower price point.
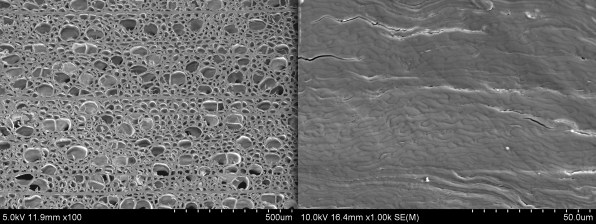
The properties of this “superwood,” as the research team at the University’s A. James Clark School of Engineering calls it, are quasi-magical.While the superwood is as strong as steel, it is six times lighter. Team co-leader and professor of mechanical engineering Teng Li also pointed out that “it takes 10 times more energy to fracture than natural wood.” To give you one example of how hard that is, the team fired bullets against two pieces of the same type of wood and while the bullet pierced the untreated wood completely, the superwood block, of the same thickness and size, stopped it completely.
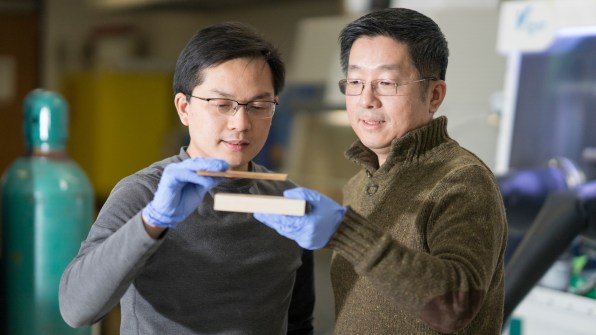
Li also added that the manufacturing process is easy and inexpensive, allowing you to treat any type wood–even soft balsa wood–in bulk on the cheap. Before the process begins, you can even mold or bend the material to adopt any shape you want.The treatment process begins by removing the lignin from the wood–the substance that makes it rigid and brown. Then, the wood is squeezed at 150 degrees Fahrenheit, compressing its cellulose so tightly that it reduces its thickness to one-fifth of its size. The key in the entire process, the paper explains, is the concentration of lignin. Professor at the Finnish Aalto University Orlando J. Rojas, who reviewed the paper independently, says that “too little or too much removal [of lignin] lowers the strength compared to a maximum value achieved at intermediate or partial lignin removal.” At the end of the process, the compression of the fibers has created an extremely strong hydrogen bond, which is what gives the superwood its super strength.
It almost seems too good to be true, given the abundance and low cost of so many fast-growing trees. Imagine the kind of furniture or custom structural pieces you can build without having to incur the high costs of carbon fiber or titanium alloys. According to Brown University’s Dr. Huajian Gao–who is not associated with the study–this supermaterial has all the features needed to be “used in cars, airplanes, buildings–any application where steel is used.”
My mind is spinning with the possibilities for engineers, industrial designers, and makers of pirate peg legs.
Source: CO.DESIGN, February 2018