[Photo: Skyscrape]
BY ADELE PETERS
Source: www.fastcompany.com February, 2020
Instead of adjusting your thermostat, your clothes may soon just adjust themselves.
If you step into a warm building on a cold day, the fabric in this new jacket will transform itself in response to the change in temperature—so you can leave the jacket on without overheating. When you go outside again, the fabric will change back, providing more insulation to keep you warm.
Inside the fabric, a new type of yarn is what’s doing the transforming. “The yarn was structured to have an exaggerated response to temperature, so it expands or contracts a lot when the temperature changes,” says Brent Ridley, CEO and founder of Skyscrape, the company developing the fabric and a new line of clothing that uses it, beginning with the jacket. The new yarn is combined with a conventional yarn, and as the new yarn expands, it makes the structure of the fabric bend—moving from a flat shape to a wavy shape like the inside of corrugated cardboard. The little pockets of air that form result in more insulation.
If a traditional jacket might be comfortable to wear within a 10- to 15-degree temperature range, the new jacket has a range of 20 to 30 degrees. “We’re focused on mitigating larger temperature changes that we all experience when we moved from indoors to outdoors,” Ridley says. “And especially as we’re moving through cities and suburbs, [as in] transitioning between a subway car and the outside world as we walk to the next destination.”
The yarn is created without any batteries or wires or sensors; it can use ordinary materials and textile machinery, but tweaks the usual process on those machines. (When the startup first began talking with textile manufacturers about the process, Ridley says, the first response was always, “Why would you want to do that? You really don’t want to do that.”) It involves tweaking the machinery to manipulate the “four Ts” of making yarn—time, temperature, tension, and twist. Then the new yarn can be combined with conventional yarn and made into fabric for finished garments. In one design that the company is considering, all of the components of the jacket are made from polyester, so that it can easily be recycled.
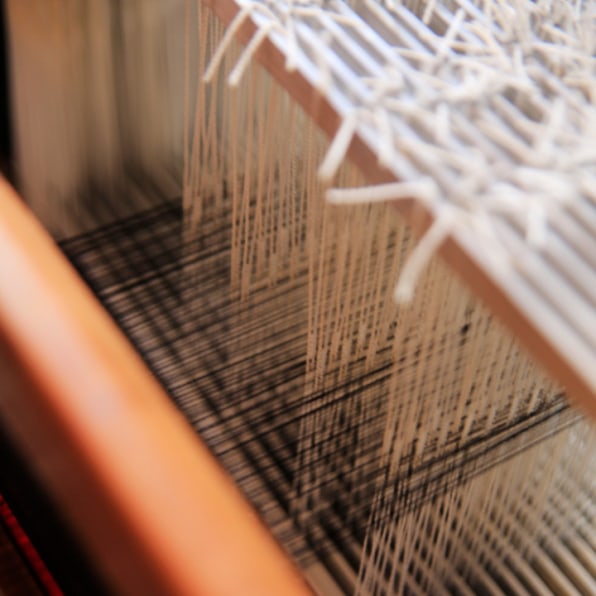
While the startup is launching first with outerwear that can worn inside and outside, the same material also has potential for indoor-only garments. The technology, which was first developed at the San Francisco-based research and product development company Otherlab before spinning off into the startup, was initially conceived as a way to save energy. Wearing the fabric has the same effect as adding an extra sweater without the inconvenience of changing clothes, so people can turn down the thermostat. ARPA-E, the government agency that funds advanced energy research, funded the initial development. “The government motivation was really borne out of a recognition that a small change in how people heat and cool buildings can lead to a pretty large change in domestic energy use,” Ridley says.
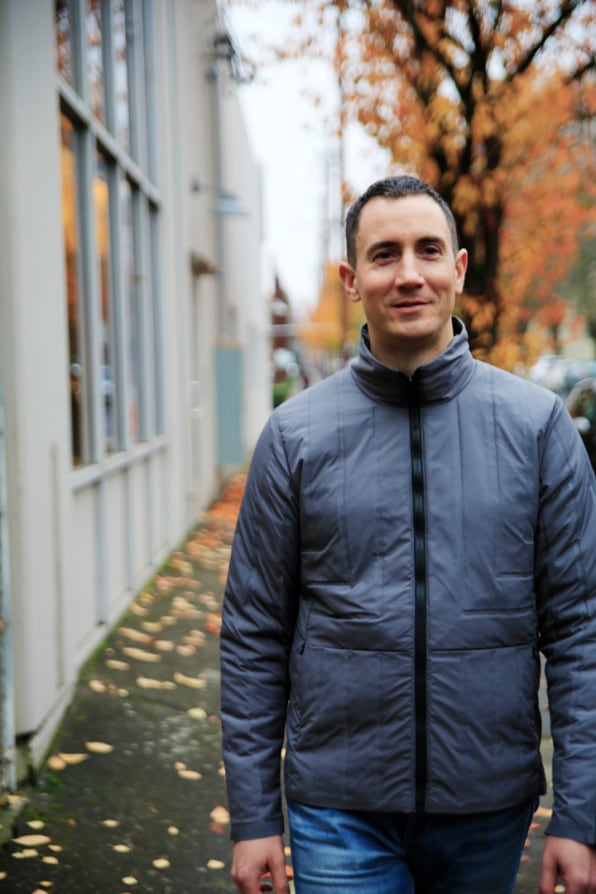
The startup is working with manufacturing partners now, and plans to scale up to begin its first large fabric production runs in the coming months. A limited number of garments will be produced by the end of the year. When the first products come to market—likely both in partnership with existing outdoor brands, and in the company’s own direct-to-consumer line—the price will be comparable to high-end “technical” jackets. “Hopefully what we’re going to make is an heirloom piece that will last for a long time and will justify that higher price point,” Ridley says. In theory, the versatility might also mean that people can buy fewer clothes. “A single garment might take the functional role of two in somebody’s closet.”